Share this
Flip Cap supplier success factors for QA & Compliance: making the right choice
by Ewan on Apr 11, 2024 2:29:42 PM
Ensuring product integrity and patient safety is the aim of the whole pharmaceutical industry. This responsibility extends to every component of pharmaceutical packaging, including seemingly minor elements like flip caps. Flip caps play a critical role in the usability, safety, and integrity of pharmaceutical products. Therefore, selecting the right flip cap supplier is an important decision for Quality Assurance (QA) managers in pharmaceutical laboratories. This article explores the key success factors to consider when choosing a flip cap supplier, focusing on quality, compliance, and reliability to meet the requirements of this industry.
I. Understanding the Importance of Flip Caps in Pharmaceutical Packaging
The role of flip caps extends beyond just sealing a container. They are integral to the product’s lifecycle, affecting everything from production to patient use.
- Protection: Flip caps are maintaining the sterility and integrity of pharmaceutical products. They prevent external contamination from microbes, dust, and other environmental factors, ensuring the medication remains effective and safe for consumption. The design of the flip cap also plays a role in protecting the product from physical damage during transportation and handling.
- Convenience: Ensuring ease of use for the end-user is a primary function of flip caps. This includes considerations for ergonomics and accessibility, allowing patients of all ages and abilities to open and close the packaging without difficulty. The design must balance child resistance with the need for senior-friendly access, a challenge that requires innovative engineering.
- Compliance: Flip caps must comply with strict regulatory standards that ensure safety and efficacy. These standards cover child resistance, senior-friendly access, and the materials' compatibility with the pharmaceutical product. Compliance ensures that the packaging meets global safety standards, facilitating wider market access.
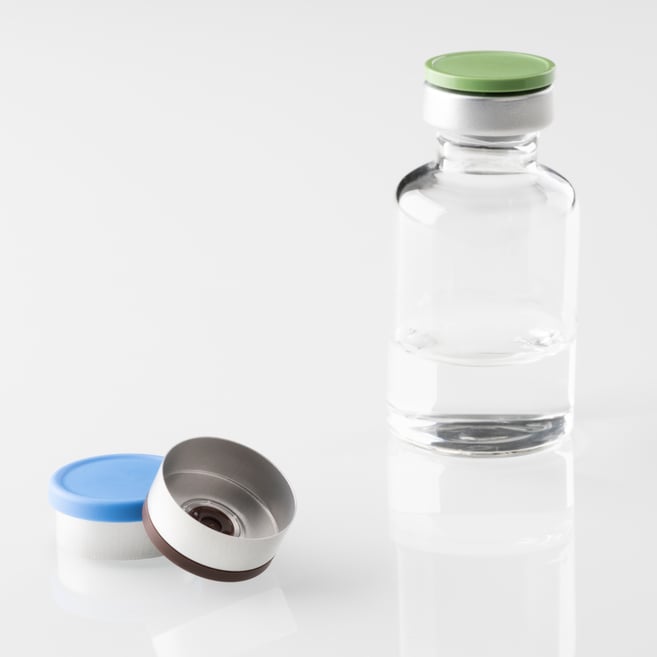
II. Criteria for Selecting a Flip Cap Supplier
Selecting the right flip cap supplier involves a comprehensive evaluation of their capabilities and practices.
A. Quality Assurance Practices
- Certifications and Standards: Suppliers should have certifications such as ISO 9001, which demonstrates a commitment to quality management systems, and ISO 15378, specific to primary packaging materials for medicinal products. These certifications indicate that the supplier adheres to international standards for quality and safety in pharmaceutical packaging.
- Quality Control Measures: This includes rigorous inspection processes, established quality control metrics, and low defect rates. Suppliers should have transparent processes for identifying and addressing quality issues, ensuring consistent product quality.
B. Compliance with Pharmaceutical Regulations
- Material Safety and Compatibility Compliance with USP Class VI and European Pharmacopoeia standards is essential for material safety. These standards ensure that the materials used in flip cap production are biocompatible and do not react adversely with the pharmaceutical product, maintaining its efficacy and safety.
- Child-Resistant and Senior-Friendly Features: Adherence to standards such as the CPSC (Consumer Product Safety Commission) guidelines and ISO 8317 for child-resistant and senior-friendly packaging is mandatory. These regulations ensure that packaging is accessible to the intended users while preventing accidental access by children.
C. Supply Chain Reliability and Scalability
- Production Capacity: The supplier's ability to meet demand fluctuations without compromising quality is critical. This includes having scalable production capabilities to respond to market demands and potential scale-up requirements.
- Logistical Efficiency: On-time delivery rates and supply chain transparency are vital. Suppliers should have reliable logistics and distribution networks to ensure timely delivery of flip caps, preventing disruptions in the pharmaceutical product’s market supply.
D. Innovation and Technological Advancement
- R&D Capabilities: Investment in research and development is key for continuous improvement of flip cap designs. Suppliers with strong R&D capabilities can offer innovative solutions that improve packaging functionality and compliance with evolving regulatory standards.
- Customization Options: The ability to tailor flip cap solutions to specific packaging needs allows for greater flexibility in product design and functionality. Customization can address unique product requirements, enhancing user experience and compliance.
III. Evaluating Supplier Performance and Partnership Potential
Choosing a flip cap supplier involves thorough evaluation beyond immediate product needs. It requires assessing the supplier's track record, financial health, and the support infrastructure they offer.
A. Case Studies and References
Suppliers should provide case studies or references that showcase successful collaborations with pharmaceutical companies. These references are valuable for understanding the supplier's capability to meet industry-specific standards and adapt to client needs. Look for stories that detail the supplier's role in overcoming complex packaging challenges, their flexibility in meeting tight deadlines, and their commitment to maintaining high-quality standards under regulatory scrutiny. These examples serve as tangible proof of the supplier's reliability and expertise in the pharmaceutical packaging field.
B. Financial Stability and Business Continuity Planning
- Resilience to Market Fluctuations: In an industry where regulatory, market, and economic conditions can change rapidly, the financial stability of a supplier is paramount. Assessing a supplier's financial health can be done through financial audits, credit ratings, and by reviewing their history of sustained operation and growth. A stable supplier is more likely to withstand market downturns and maintain consistent supply chains.
- Business Continuity Planning: Evaluate the supplier's preparedness for unexpected events, such as natural disasters, pandemics, or supply chain disruptions. A robust business continuity plan indicates the supplier's ability to ensure uninterrupted supply, which is crucial for maintaining the pharmaceutical production schedules and market commitments. Ask for details on their backup manufacturing sites, alternative supplier networks, and strategies for logistics challenges to gauge their resilience.
C. Customer Support and Technical Assistance
- Support for Product Integration and Compliance: The ideal supplier offers comprehensive support services that facilitate easy integration of their flip caps into your existing product lines, while also ensuring compliance with regulatory standards. This includes providing detailed product specifications, compatibility guidance, and regulatory documentation support.
- Responsive Troubleshooting and Technical Assistance: Availability of prompt and effective customer support for addressing any operational issues is critical. The supplier should have a knowledgeable technical support team that can assist with troubleshooting, offer solutions for improving packaging performance, and provide updates on regulatory changes affecting packaging requirements.
IV. Making the Right Choice: A Step-by-Step Guide
The process of selecting the right flip cap supplier is critical to ensuring product quality, regulatory compliance, and supply chain reliability. Follow this step-by-step guide to make an informed decision.
A. Define Your Specific Needs and Requirements
- Product Specifications Alignment: Begin by clearly defining the physical and chemical specifications of your pharmaceutical product. This includes understanding the product's sensitivity to light, air, or moisture, which will influence the type of flip cap required. Consider the dimensions, material compatibility, and any unique features (e.g., tamper-evidence, child-resistance) that the flip cap must possess to ensure both product integrity and user safety.
- Regulatory Requirements Compliance: Identify all relevant regulatory requirements for your product's packaging. This involves not only current regulations in your target markets but also anticipating changes in legislation. Ensure that the flip cap features align with guidelines provided by all relevant bodies. These requirements might include specific material standards, child-resistance and senior-friendly opening mechanisms, and tamper-evidence features.
B. Conduct a Comprehensive Market Survey
- Industry Databases and Directories: Utilize industry-specific databases and directories to compile a list of potential suppliers. These resources can provide a wealth of information, including supplier specialties, certification statuses, and previous client reviews.
- Trade Shows and Professional Networks: Attend industry trade shows, seminars, and conferences. These venues offer opportunities to meet suppliers face-to-face, observe product demonstrations, and collect business cards for future reference. Networking with peers can also yield recommendations and insights into suppliers' reputations and performance.
C. Perform a Rigorous Supplier Evaluation
- Criteria-Based Assessment: Assess potential suppliers against the detailed criteria established earlier in this guide, including quality assurance practices, compliance with pharmaceutical regulations, supply chain reliability, and innovation capabilities. This comprehensive evaluation should include reviewing certification documents, quality control records, and regulatory compliance proofs.
- Site Visits and Sample Testing: Arrange for site visits to the suppliers' manufacturing facilities to observe their operations firsthand and verify their compliance with quality and regulatory standards. Request sample flip caps for testing with your products to ensure compatibility and meet all specified requirements.
D. Negotiate Terms and Establish a Partnership
- Long-Term Collaboration Focus: When negotiating with suppliers, emphasize the importance of a long-term partnership. Discuss not only pricing and delivery terms but also how you can work together towards continuous improvement in product quality, compliance, and innovation.
- Terms and Conditions: Finalize terms that cover pricing, delivery schedules, minimum order quantities, and payment terms. Include clauses for regular quality reviews, compliance updates, and the mechanism for handling defects or non-compliance issues.
- Continuous Improvement Mechanisms: Agree on mechanisms for ongoing product development and improvement, ensuring that the flip cap design can evolve in response to new regulations, market demands, or technological advancements.
Conclusion
Selecting the right flip cap supplier is a critical decision that impacts product quality, patient safety, and regulatory compliance. By considering the factors outlined in this article, QA managers in pharmaceutical laboratories can make informed choices, ensuring their packaging components meet the highest standards of quality and reliability. Remember, the goal is not just to find a supplier but to establish a partnership that will contribute to the success and sustainability of your pharmaceutical products.
To help you, here’s a checklist of your Step-by-Step Guide:
- Define Your Needs and Requirements
- Product Specifications Alignment
- Regulatory Requirements Compliance
- Conduct a Market Survey
- Industry Databases and Directories
- Trade Shows and Professional Networks
- Perform a Supplier Evaluation
- Criteria-Based Assessment
- Site Visits and Sample Testing
- Negotiate Terms and Establish a Partnership
- Long-Term Collaboration Focus
- Terms and Conditions
- Continuous Improvement Mechanisms
No Comments Yet
Let us know what you think